At XSF, Quality Matters Most
The design and manufacturing of Aluminum Trusses, Towers, and other Rigging Accessories isn’t as straightforward as you might think.
Every step of the process needs to be handled meticulously with attention to detail in order to prevent errors and maintain the highest possible Quality Standards.
As a trusted producer of Aluminum products for the Entertainment Industry, XSF has developed a solid quality control process that we have relied on for years to ensure the best performance of both our management team and our production personnel.
In this article, we hope to offer a glimpse of what our quality control manual looks like in order to demonstrate the depth of the measures we take in order to manufacture only the best.
XSF Quality Control Truss Fabrication and Manufacturing Video
This video takes you on a walk-through of the XSF Facility and the details inside our XSF Quality Control Process.
The Benefits of Our Quality Control Process
1. Safety and Equipment
With the operation of heavy machinery, the potential danger from malfunctioning equipment is not to be overlooked.
For this reason, the XSF procedure is both straightforward and highly effective in this matter.
In addition to always keeping equipment clean and well maintained, we require that any piece of equipment found to be needing repairs be immediately reported to the foreman.
It may not be returned to service until it has been satisfactorily repaired.
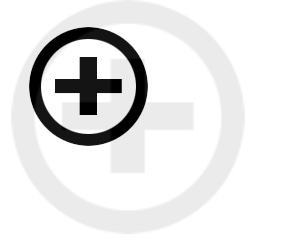
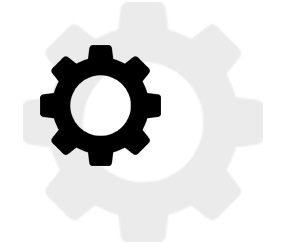
2. Fabrication Drawings and Engineering
The process of moving projects from the design stage to fabrication is developed in order to make sure the customer’s specifications are met while ensuring the highest quality of design.
The steps involved can be summarized as follows:
- The XSF design team prepares the design drawings, working with the customer, a third party structural engineer, and the sales team on any revisions if necessary.
- Once approved they will be converted to fabrication shop drawings. The Vice President of Production and the shop foreman must approve these plans prior to fabrication. Any changes required are noted on the drawings and submitted to the customer by the sales representative for approval.
- The shop foreman is responsible to to ensure that all shop staff are aware of any revisions.
3. Raw Materials: Receiving and Inspection
In order to maintain consistent quality through every stage of fabrication, all staff are responsible for visually inspecting materials as they pass through the process.
When raw materials are received from the mill, they must be compared to the purchase order before a receipt is signed.
All materials should be handled with care and stacked in a safe and organized manner.
Raw aluminum must be inspected for defects before it is stored, with any defective pieces being separated and clearly marked as such, and reported to the Shop Foreman or Vice President of Production.
To ensure the quality of everything XSF manufactures, all raw materials include mill certification reports available upon request that verify the materials are of the correct grade and meet XSF’s strict requirements.
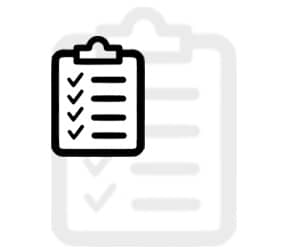
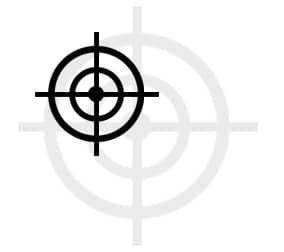
4. Fabrication: Precision Cutting and Machining Parts
Maching and saw cutting personnel are responsible for adhering to the specifications of the fabrication drawings, and must inspect each component as they are being prepared for the welding line.
Questions are to be directed to the shop foreman and/or the design team.
Scrap materials are always to be recycled—NOT reused for fabrication.
Likewise, any materials that are defective but may look to be complete must be visually marked as defective on the outside in order to prevent accidental usage.
Saw cutting personnel must sign and date the XSF quality control tag to verify their inspection before any parts are to be passed on to the welding line.
5. Fabrication: Welding
Welding is an important step of the process, and XSF takes every precaution necessary to assure quality at this stage.
For starters, every welder at XSF must be certified according to the standards of the American Welding Society, as verified by the Shop Foreman or Vice President of production.
Furthermore, on certain projects a third party Chief Welding Inspector may be called in to inspect the quality of work.
Every step of the welding process is completed with care, and it is the responsibility of each welder involved to visually inspect their work after completion.
Unsound welds must be repaired or replaced. Before moving a welded component on to the next stage of fabrication, all welders who have worked the piece must sign the XSF quality control tag.
If any additional non-destructive testing is required, it will be carried out by the Chief Welding Inspector.
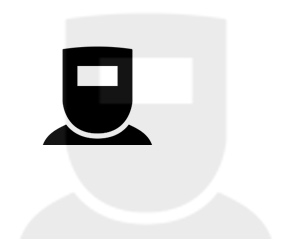
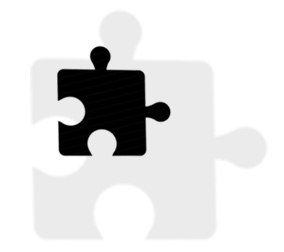
6. Final Assembly and Test Fit
If necessary, trusses will undergo final assembly and test fit in the shipping and receiving area.
Test fits are always required for custom trusses.
At this stage, the truss is inspected for errors or omissions and compared to fabrication drawings to ensure compliance.
As expected, everyone involved at this stage will be responsible for signing the quality control tag.
7. Cleaning and Inspection
Once fabrication is complete and the items have been test fit, each component will be cleaned, visually inspected for missing welds, errors or omissions, and prepped for packaging or coating.
Before, during, and after cleaning and inspection, trusses should always be handled and stacked with care to avoid unnecessary wear on the product.
All staff involved again sign off on the quality control tag.
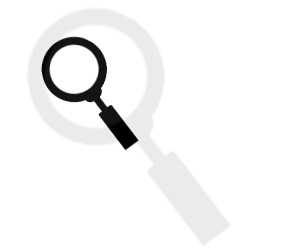
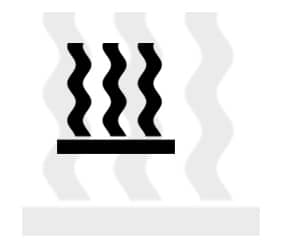
8. Coatings and Surface Finishes
Coatings are typically provided by an outside vendor and inspected by XSF staff before moving on in the fabrication process.
Additionally, steps need to be taken to ensure that all corrosive materials are removed before packaging.
Inspection must ensure that the coating is in compliance with fabrication drawings, with any deficiencies in color, damage, peeling, etc. to be reported to the shop foreman and corrected by the vendor.
9. Identification, Packaging, and Shipping
Every truss or component fabricated by XSF is marked with a product sticker that includes important information such as the manufacturing date, serial number, engineered load table, etc.
The XSF quality control tag, which indicates all of the staff involved in fabrication, is also to remain attached to the final product.
Appropriate steps are to be taken to ensure quality packaging. Individually shipped trusses are packaged separately, while bulk orders may be packed directly on to trucks, with shipping blankets and other measures used to ensure safe travel. XSF will work with the customer to arrange the best shipping to meet their needs.
If the customer is picking up, XSF will load the truck if desired and offer advice on safe transport.
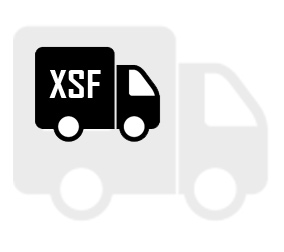
As you can see, there is a lot that goes into quality assurance at XSF. Every step of the process is meticulous.
We’ve created a procedure that helps us prevent errors in fabrication as much as possible, and find them quickly when they do occur.
All this adds up to one thing: better products for the customer—because at XSF, quality matters most.
Contact Us Now!