Selecting Aluminum Truss in the Global Market
The skies were clear over Toronto in 2012 when Radiohead was preparing to perform at Downsview Park and the stage crew was erecting the aluminum truss structure over the stage. Drum tech Scott Johnson was just doing his job when, according to the engineering report, the pick-up trusses that support the roof and lighting collapsed under the weight of load, killing the 33-year-old and injuring three other people.
Doug Perovic, a forensic engineer from the University of Toronto who, along with a team of engineers, investigated the accident, said that the pick-up trusses that were used in the rig were not part of the original design.
The report issued by the Ontario Ministry of Labour did not elaborate on the nature of the trusses that were substituted, but it’s interesting to note that they were interchangeable with the original trusses, yet they were not able to withstand the weight of the stage grid.
These trusses were obviously not the right tool for the job.
Written By: Richard Cadena
More about Richard at the bottom of this page.
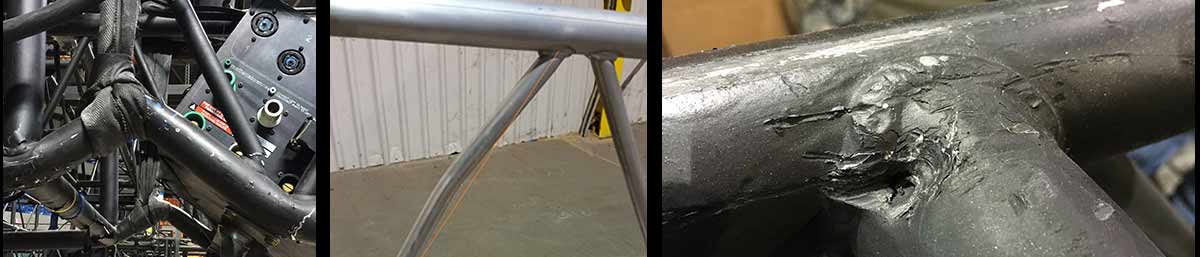
How can we prevent these types of accidents in the future?
The answer to that question is multi-faceted and it’s an important topic in the global truss market, and the solution starts with the selection of the right aluminum truss.
Like any structure designed to bear weight, stage truss should be designed according to standard engineering practice. If a licensed professional engineer puts his seal on a design, it has to comply with a number of standards that cover important safety issues such as the maximum allowable stress of aluminum structures, the design of load-bearing structures, the specification of aluminum alloys for drawn, seamless tubes, construction techniques, and other safety standards.
Certified Welders: The Importance of AWS Certification
Another very important aspect of stage and lighting truss is the quality of the welds. In the manufacture process, every welder involved in the production should be certified. There are organizations that offer certification programs to recognize and document the knowledge and expertise of welders, and in North America, that organization is the American Welding Society (AWS).
The certifications are performance-based, so, in order to be certified, a welder has to demonstrate proficiency in a particular type of welding and pass a written exam. If a manufacturer of stage truss cannot provide proof of certified welders, there is no guarantee that the quality and the integrity of the welds meets the requirements for a safe structure.
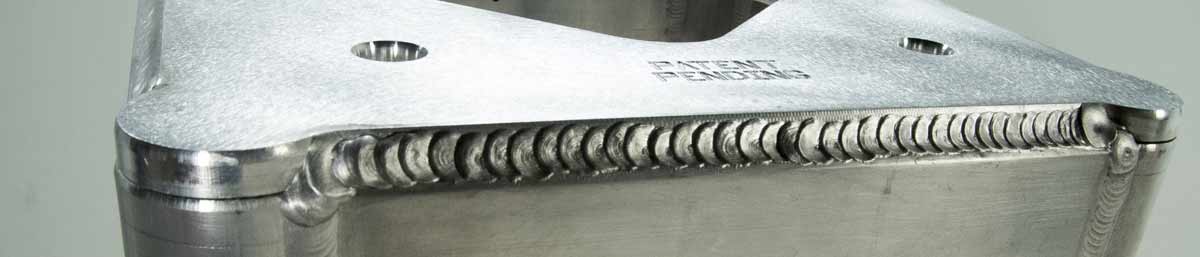
Quality Control: Maintaining Quality in the Fabrication of Truss
When the truss is fabricated, the welds should be inspected by a certified welder who has the knowledge to evaluate the quality of the welds. There are standards set forth by the AWS, and any welds that do not meet the criteria should undergo a non-destructive test like a liquid dye test where the penetration of the dye reveals any pores or weaknesses in the weld. A good weld is uniform in width, height, and color, and has no splatter. It has a distinct look that a trained eye can recognize.
If a manufacturer has a good quality control procedure in place, there are red flags that should trigger a work stoppage. Each weld should be reviewed by more than one person—preferably several people—to make sure that an inferior weld does not make it past QC. The QC procedure should be well documented by the manufacturer and the documentation should be available to end users on demand. If a truss manufacturer cannot provide it, then the buyer should beware. Stage truss is often used over people’s heads, and every safety precaution should be heeded if we are to prevent accidents, and the quality of each and every weld is of utmost importance.
Evaluation and Testing: Confirming the Design of Truss
In addition to meeting certain design criteria, a properly engineered aluminum truss or lighting truss system should undergo evaluation confirm the design and testing to confirm its performance under both static and dynamic loads. The design can be evaluated using software that models the truss in the virtual world, and this virtual test is sometimes followed by a real-world physical test to confirm the calculations.
Some are destructive tests and others are non-destructive tests. A destructive test is where a structure is loaded beyond its capability in order to determine the point of failure.
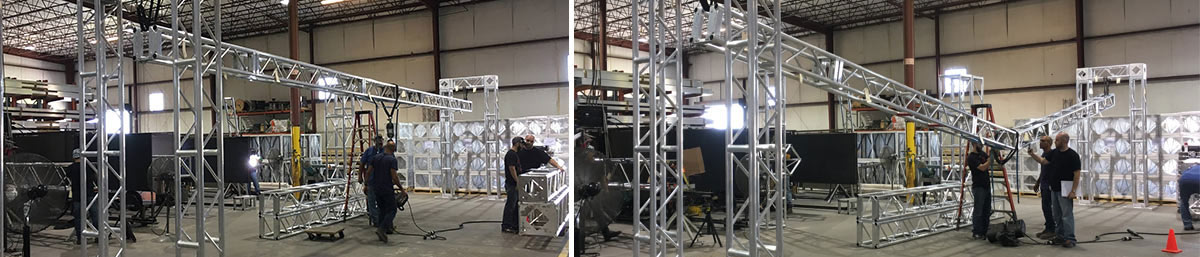
Truss Load Tables
When stage truss is engineered properly, it is modeled in software and calculations are made in order to evaluate how much weight it can support for a given uniformly distributed load or point load at a given span of truss.
From these calculations, load tables are generated that provide information for the end-user in the field. Load tables always include a safety factor of 1.95 for truss, meaning that the truss should be able support 1.95 times more weight than indicated by the loading table.
Responsible truss manufacturers should be able to provide current load tables for all of their products, and the load tables should be backed by engineering reports that include the name of the engineer and the engineering firm, and the date of the report.
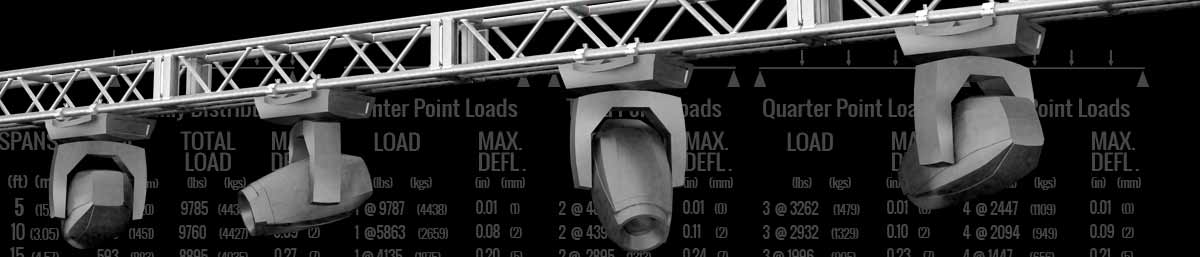
Packaging: Protecting Truss During Shipment
How a truss is packaged is as important as how well it’s made. The ANSI standard for the design, manufacture, and use of aluminum truss and towers (ANSI E1.2) says that every stage truss section should be inspected when it arrives from the manufacturer, even when it is purchased brand new. The truss should be inspected for twisting, racking, or bending of the truss, dents, bends, or abrasions in the truss chords and diagonals, flatness or deformation of the connection plates (if any), deformation of the pinned connector forks (if any), and cracks, breaks, or deformation of the welds. The fasteners should also be inspected for the proper grade of hardware excessive wear, and deformation.
If truss is packaged and shipped properly, then it should arrive without any of these issues; however, should it arrive damaged, the damage should be documented, and a claim filed.
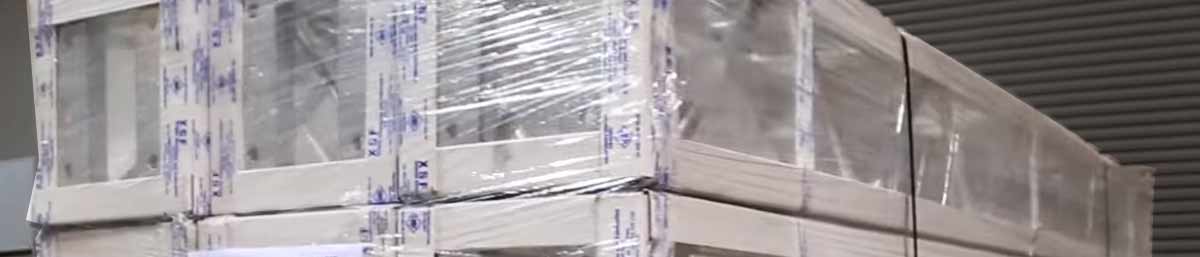
Liability: Who Pays?
In the unfortunate event of an accident involving a truss structure in which people are injured or killed, there will be a lawsuit and liability will be assigned in a court of law. A lawsuit is based on negligence, and according to Black’s Law Dictionary, negligence is “the omission to do something which a reasonable man, guided by those considerations which ordinarily regulate the conduct of human affairs, would do, or doing something which a prudent and reasonable
man would not do.” A reasonable person, it could be argued, would use properly engineered truss if they are undertaking potentially dangerous work like rigging thousands of pounds over people’s heads. If the truss involved in the accident cannot be proven to be properly engineered by producing documentation, the owner of the truss could be found negligent. Liability could also be assigned proportionally between the manufacturer, distributor, and end-user, depending on the circumstances.
If the manufacturer is a foreign company, it will be difficult to involve them in a lawsuit,
so the liability will fall back on the distributor and the end-user.
Minimizing Accidents with Truss
The best defense against accidents involving truss structures is to select the right components and use them properly. Unfortunately, the live event production industry has a long history of staging accidents, and most of them involve inferior products and/or improper use of truss structures.
If you select your components properly and use them as specified by the manufacturer, the likelihood of accidents will be greatly reduced.
There are a number of products on the market from which to choose, many of which look like every other product. It’s incumbent upon the end-user to investigate the quality of the products they use, including seeking out documentation that backs up claims about loading tables, quality of the materials and welds. Should you follow these guidelines, in the unlikely event of an accident, you will have much less exposure to liability.
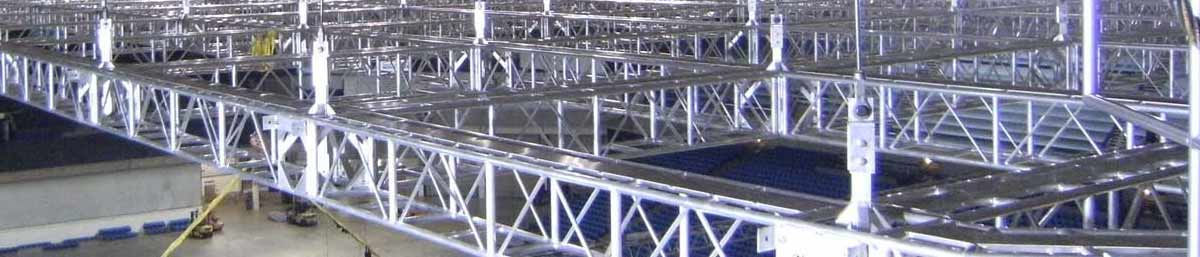
About the Author:
Richard Cadena is an ETCP Recognized Trainer and an ETCP Certified Entertainment Electrician with 30 years of experience in the live event production industry. He is the author of:
- “Automated Lighting: The Art and Science of Moving and Color-Changing Light, 3rd Edition”
- “Electricity for Entertainment Electricians & Technicians, 2nd Edition”
- “Lighting Design for Modern Houses of Worship”
- “Focus on Lighting Technology”
As a freelance lighting designer and lighting consultant he has worked on concert tours, television, theatre, motion picture productions, and he has designed dozens of lighting systems for permanent installations. He is also the technical editor for PLASA Media and a columnist for Lighting & Sound America, Lighting & Sound International, and Protocol magazines. He is a member of IATSE Local 205 in good standing.